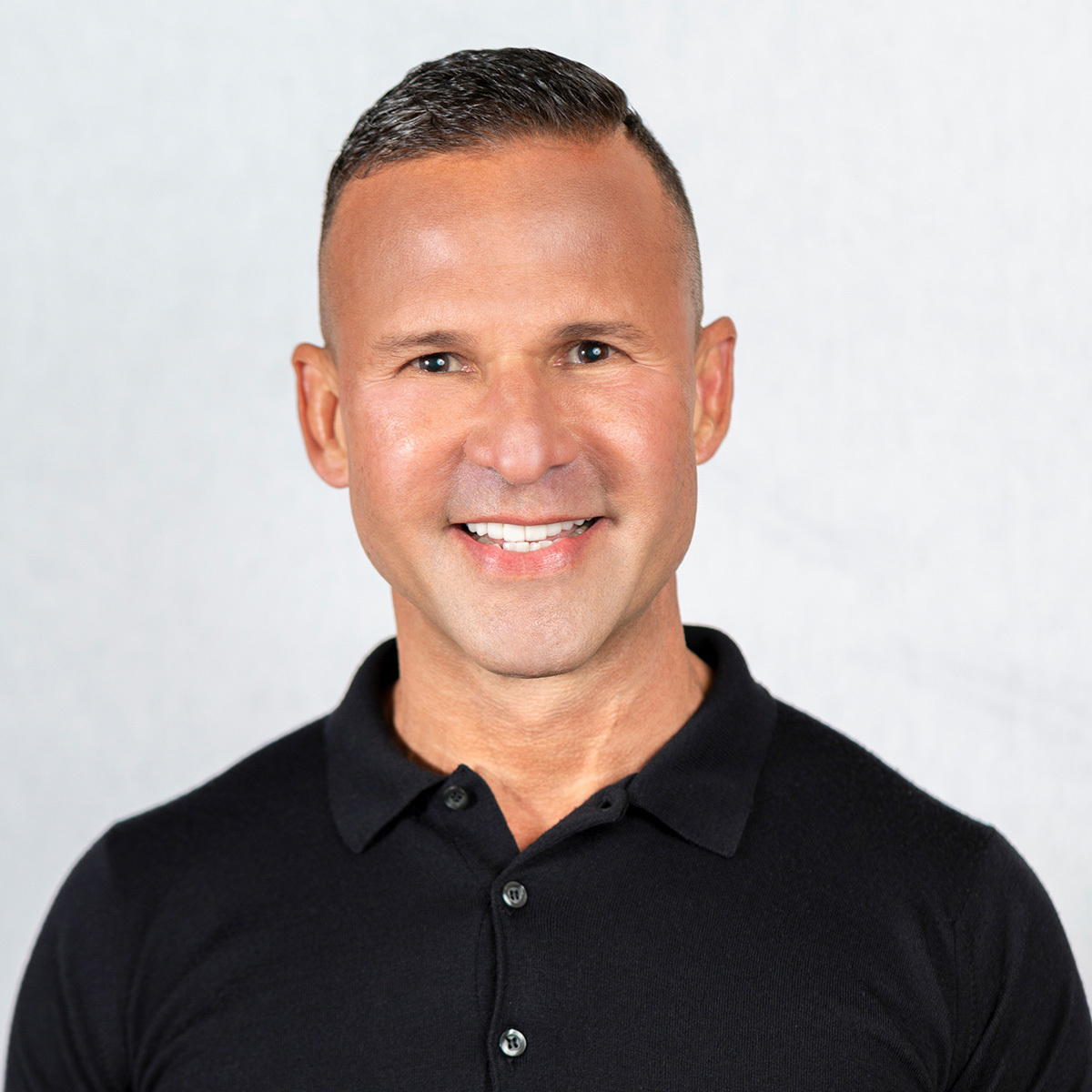
A Letter from the CEO
At Kraft Heinz, our Company Dream is To be the leader in elevating and creating food that makes you feel good. It’s the North Star that points our way forward. We believe in making food that nurtures your body and warms your SOUL. Food that’s good for your HEALTH, and good for our PLANET. Food that delivers good VALUE, with QUALITY you feel good about serving to the people you love.
On behalf of our 36,000 global employees, I welcome you to our 2024 Environmental Social Governance (ESG) Report. We share it to update you on the progress we are making toward our ESG goals, working Together at the Table with our stakeholders to help solve some of the most pressing issues facing our industry – and our world.
We center our enterprise-wide ESG efforts around three Pillars: Healthy Living & Community Support, Environmental Stewardship, and Responsible Sourcing. ESG initiatives are integrated into our long-term business strategy, whether we are sustainably sourcing tomatoes for our beloved Heinz Tomato Ketchup, supporting the communities where we work and live, improving product health and nutrition, or procuring electricity from renewable sources. Our efforts focus on the priority areas and issues where we believe we can make the most impact on the planet, business, and brands.
As we have highlighted in our past ESG Reports, partnerships are essential to achieving our ESG goals. For example, in 2023 we hosted our first-ever supplier webinar to share our ESG strategy and Net Zero ambition and set the foundations for a future Supplier Sustainability Engagement program. We also announced a new goal to reduce the use of virgin plastic in our global portfolio by 20 percent by 2030 – something only possible through collaboration with our packaging partners. And one of our most vibrant long-term partnerships is with Rise Against Hunger, as we work together to alleviate global hunger. In 2023, we provided approximately 368 million meals to people in need, achieving 90 percent of our goal to provide 1.5 billion meals to people in need by 2025.
As we look ahead, what will drive our ESG agenda is our Company’s new 10-Year Strategy (10YS). It is guiding our path forward, as well as our strategic platforms, markets, and investments.
The timeline for the majority of our current ESG commitments is 2025. To align our ESG commitments with our business strategy, we will evaluate our current progress and future goals through the lens of our 10YS with a focus on topics that we can directly influence and that are important to business resilience.
Like many of our peers, as we near the midpoint of the decade, we are more aware of the challenges of delivering our ambitious ESG goals. At Kraft Heinz, we are working diligently to address our biggest challenges and making substantial improvements as we press toward our ESG goals. That’s what a spirit of Ownership is all about.
We’ve learned a lot over the past five years and commit to continuing to learn and improve. It’s all about setting the table for the future – one that is more delicious and sustainable for us all. As we look to the future, we aim to continue to build a robust, improved ESG agenda centered around strategic commitments and focused delivery to drive both ESG performance and stockholder value.
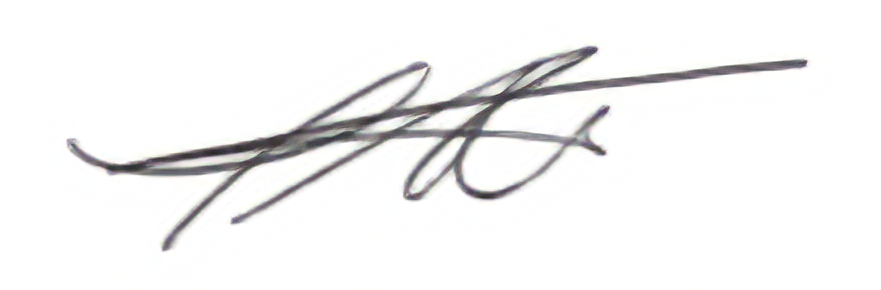
Carlos Abrams-Rivera
Chief Executive Officer and Member of the Board of Directors
The Kraft Heinz Company
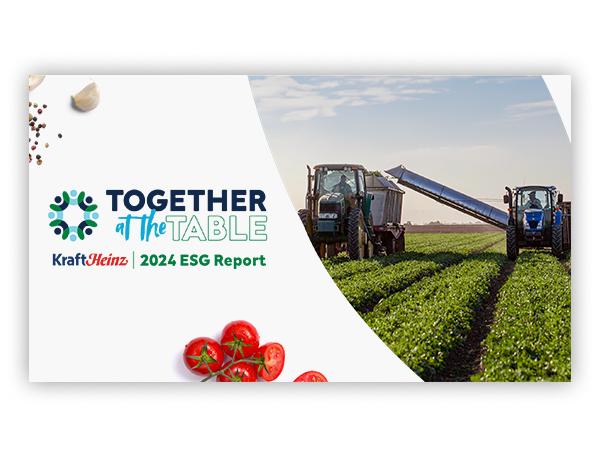
Download the Report
This Report reflects our commitment to transparency and provides details for our stakeholders on progress to date against our ESG goals and objectives, which are based on our most material issues.